News
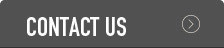
Jiangsu province Wuxi city Huishan District Yuqi Industrial Park
Contact:Mr. Ding
Mobile:+86 13606198962
Contact:Ms. Tang
Mobile:+86 13701511238
Tel:0510-83586958,83886386,83890958
Fax:0510-83586358,83586958
E-mail:fh@wuxifh.com
http://www.wuxifh.com
Contact:Mr. Ding
Mobile:+86 13606198962
Contact:Ms. Tang
Mobile:+86 13701511238
Tel:0510-83586958,83886386,83890958
Fax:0510-83586358,83586958
E-mail:fh@wuxifh.com
http://www.wuxifh.com
Knowledge
Position:首页 > NEWS > Knowledge
Spray drying process of centrifugal spray dryer
Update time:2017-03-01 22:47:29Clicks:4082
Centrifugal spray dryer adopts high-speed centrifugal atomizing disc movement, the material atomized into droplets, and after the hot air enters into the tower body of the special distribution in trajectory matching and heat exchange, in a very short time
Centrifugal spray dryer adopts high-speed centrifugal atomizing disc movement, the material atomized into droplets, and after the hot air enters into the tower body of the special distribution in trajectory matching and heat exchange, in a very short time to evaporate moisture, forming uniform powder dry product. Centrifugal spray dryer is widely used in chemical, food, pharmaceutical, petrochemical, light industry, pesticide and other industries.
Centrifugal spray drying speed, liquid surface area increased significantly after the spraying, in the hot air, can instantly evaporate 95% - 98% water, drying time in just a few seconds, particularly suitable for drying heat sensitive materials. The product has good uniformity, fluidity and solubility, high purity and good quality. The production process is simple, easy to operate and control. For the moisture content of 40-60% (special materials up to 90%) of the liquid can be dried into a powder product, dry without crushing and screening, reduce production processes, improve product purity. The product particle size, loose density, moisture, in a certain range can be adjusted by changing the operating conditions, control and management are very convenient.
Spray drying process is entirely dependent on the composition of the product. Some are very easy and others are very hard to dry.
The total moisture content of the discharged air is one of the most important parameters. Depending on the composition of the product, for example in the discharge total amount of moisture in the air, can be dry products with high protein content, high carbohydrate content and low moisture content requirements, in order to avoid sticking in the chamber, pipeline and cyclone powder.
This is also why the total moisture content in the ambient air is an important parameter to know the design of the former plant, as a decrease in the total moisture content of the surrounding environment if the drying potential is high".
Another important parameter is the maximum solids content in the concentrate. This is the viscosity driven and therefore also depends on the composition of the product. As a rule of thumb:
High fat content
Allow higher solids content.
Lower drying temperatures are required to avoid sticking (i.e., low total moisture content in the exhaust gas).
High protein content
Lower solids content required due to viscosity (except for proteolytic enzymes).
Allow higher drying temperatures (i.e., high moisture content).
The protein content is high, the more difficult it becomes the agglomeration process. However, this is offset if the MSD or IFD machine is selected.
High carbohydrate content
A higher concentration of solids (except starch, due to its high viscosity).
Higher spray drying temperatures are not allowed, if the carbohydrate is of high molecular weight (e.g., maltodextrin and starch), which results in an increase in the glass transition temperature. The moisture content of the air in the chamber can be higher when the drying powder has a higher glass transition temperature, resulting in a more economical drying.
If carbohydrate is a low molecular weight type (such as sugar, lactose and glucose syrup), it will result in the glass transition temperature, spray drying temperature it has low requirements, in order to avoid sticking (reduce the exhaust air in the lower moisture content)
Centrifugal spray drying speed, liquid surface area increased significantly after the spraying, in the hot air, can instantly evaporate 95% - 98% water, drying time in just a few seconds, particularly suitable for drying heat sensitive materials. The product has good uniformity, fluidity and solubility, high purity and good quality. The production process is simple, easy to operate and control. For the moisture content of 40-60% (special materials up to 90%) of the liquid can be dried into a powder product, dry without crushing and screening, reduce production processes, improve product purity. The product particle size, loose density, moisture, in a certain range can be adjusted by changing the operating conditions, control and management are very convenient.
Spray drying process is entirely dependent on the composition of the product. Some are very easy and others are very hard to dry.
The total moisture content of the discharged air is one of the most important parameters. Depending on the composition of the product, for example in the discharge total amount of moisture in the air, can be dry products with high protein content, high carbohydrate content and low moisture content requirements, in order to avoid sticking in the chamber, pipeline and cyclone powder.
This is also why the total moisture content in the ambient air is an important parameter to know the design of the former plant, as a decrease in the total moisture content of the surrounding environment if the drying potential is high".
Another important parameter is the maximum solids content in the concentrate. This is the viscosity driven and therefore also depends on the composition of the product. As a rule of thumb:
High fat content
Allow higher solids content.
Lower drying temperatures are required to avoid sticking (i.e., low total moisture content in the exhaust gas).
High protein content
Lower solids content required due to viscosity (except for proteolytic enzymes).
Allow higher drying temperatures (i.e., high moisture content).
The protein content is high, the more difficult it becomes the agglomeration process. However, this is offset if the MSD or IFD machine is selected.
High carbohydrate content
A higher concentration of solids (except starch, due to its high viscosity).
Higher spray drying temperatures are not allowed, if the carbohydrate is of high molecular weight (e.g., maltodextrin and starch), which results in an increase in the glass transition temperature. The moisture content of the air in the chamber can be higher when the drying powder has a higher glass transition temperature, resulting in a more economical drying.
If carbohydrate is a low molecular weight type (such as sugar, lactose and glucose syrup), it will result in the glass transition temperature, spray drying temperature it has low requirements, in order to avoid sticking (reduce the exhaust air in the lower moisture content)
- Previous article:Use and cleaning method of centrifugal spray dryer
- Next article:Trend analysis of spray dryer in the future market development
0
comments
